|
|
|
Year
Founded: 1981 Employees: 1 Shop Size:
1,000 square feet
FYI: Most
of the company’s customers want a massive entryway; WGH doors
commonly are 4 inches thick and 8 feet tall. |
|
|
|
|
|
|
“I never had any fun doing
kitchens. It was just too routine,” says Wayne Hausknecht, owner of
WGH Woodworking in Tucson, AZ. He is explaining how, after having
started his woodworking career building custom homes and then
progressing to interior millwork and casework, he ultimately decided
to specialize in custom entry doors. “I thought my skill level was
beyond spending my whole life making drawers and doors and doing
boxwork,” he adds.
Hausknecht started
building homes in Colorado and moved to Tucson in 1978, where he
worked with a builder interested in reviving adobe-style homes. The
builder had problems finding someone to do interior millwork and
cabinetry in a high-end rustic style to match the homes. So
Hausknecht took over that task, working on-site in the garage as
soon as the shell was complete. “I had done interior work for custom
homes in Colorado and had a lot of tools,” he says. “It kept me out
of the sun.”
Although the houses did
not sell as quickly as the builder had hoped and he eventually gave
up on the project, Hausknecht’s interior work had been noticed by
customers, and he had enough requests for his custom woodwork to go
out on his own. He also had a chance to buy an affordable building
that could be used as a shop. So he began his own business on Jan.
1, 1981, initially doing kitchen cabinets and built-ins as well as
doors, but soon specializing in just doors.
|
|
|
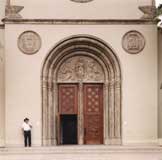 |
|
Above: Doors for the Sacred Heart church in Nogales,
AZ, were the most elaborate ones he has ever built, says Wayne
Hausknecht. He reproduced the original 80-year-old doors,
which were falling apart. The four doors are Honduras
mahogany, and each is 51 inches wide, 4 inches thick and 7
feet high. Photo by Dominic Oldershaw. |
|
|
|
|
“Doors are a lot harder than
they look, especially one-of-a-kind doors,” Hausknecht says. “A lot
of the cabinet shops recommend me, if they are too busy to do them.
And I refer cabinets and built-in work to them.”
A steady market and
consistent backlog
Hausknecht says the market for his doors has stayed steady
even through economic downturns, thanks to consistent growth in the
Tucson area, especially in upper-end homes. He works with local
contractors and architects, but mostly direct with homeowners. He
enjoys a consistent six-month backlog of jobs, which can stretch out
as long as a year.
One reason for the
backlog is that Hausknecht likes to build doors one at a time and
says that his favorite job is always “whatever I’m working on at the
moment.” While some doors are designed by an architect, most are a
collaborative effort between Hausknecht and the homeowners. He
spends a lot of time “interviewing” the homeowner, looking at their
sketches or photos to see what they like and also finding out what
woods and styles will be used on the interior of the home in order
to develop a compatible door design. Doors can range from simple,
rustic styles to elaborate designs with hand-carved elements,
“speak-easy” doors, mouldings, rosettes, grilles and other
decorations. They can take from a couple of days to eight weeks to
build, depending on how elaborate they are.
Most of his customers
are looking for a massive entryway and need an odd-sized door, which
is why they must have it custom-made. Hausknecht’s doors are often
as much as 3 or 4 inches thick and 8 feet tall. He not only designs
and builds the doors, but also does the finishing and installation.
Although Hausknecht works by himself, he sometimes hires extra help
to do installations and be able to maneuver the heavy doors
on-site.
Picking the right
woods
Hausknecht uses traditional mortise and tenon construction
and says he builds his doors to last “forever.” When it comes to
choosing the species for a project, after an initial meeting with a
customer, Hausknecht contacts different lumberyards to see what is
available, and at what price. He decides what to use, based on the
customer’s preferences and budget.
He starts a door from
the raw lumber stage, doing the rough milling himself, and says he
is very picky about the wood he selects.
“A standard door is
1-3/4 inches thick. I need to get my wood full rough, so I have to
have enough material to flatten it out and get it sanded to end up
with 1-3/4 inches. A lot of lumberyards carry lumber S2S and it’s
only 1-13/16. So I actually have to special order a lot of my wood
to bring it in full rough,” Hausknecht says. “I have to have a good
working relationship with my lumberyards, where they know how picky
I am. Because if I order lumber and they bring it in from Phoenix or
the West Coast, it has to be good or I’ll send it back.”
After the lumber is
rough milled, Hausknecht sorts through it to find boards that are
long, wide and flat enough for the stiles of the frame. “Usually I
am making the frame of the door first, because that’s the most
critical part,” he says. “The frame has to be real flat.”
|
|
|
|
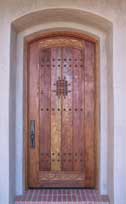 |
|
This rustic door is Douglas fir and features a
“speak-easy” door that opens behind hand-forged grillework. It
also has hand-forged nails and hand-carved decorations. The
hardware is from Rocky Mountain Hardware in Hailey,
ID. |
|
|
|
|
|
After he finds boards for the
frame, he cuts the rest of the material into smaller pieces for the
panels. This is not a random process; every piece is cut for a
certain spot so that the final product has balance and symmetry.
Hausknecht pays careful attention to the grain and color. Panel
pieces are cut from the same board, in the order that they will be
used, and all pieces are marked with arrows. “That way I can keep
everything in order and when I stain it, it will follow some sort of
pattern,” he says. “I won’t have a dark-stained piece and then a
light one and then a dark one.
“I like doing panels
one board wide or two,” he adds. “I like to do doors with no glue
lines, except for the obvious ones where the door is put together.
It’s the way doors would have been made 100 years ago, when they had
big trees.”
Hausknecht also says
that he is not afraid to waste wood in order to get the best look.
“If a piece of wood would look good in a certain area of a door and
to get it I will have a 2-foot scrap on one side and a 4-foot scrap
on the other side, I’ll cut it anyway,” he says. “I won’t try to get
two pieces of wood out of the board in order to save money or save
wood. If I cut corners, the finished product will not be what I
really want it to look like.”
In cases where
Hausknecht cannot obtain material that is thick enough for a very
thick door, he will laminate boards. “I take boards that are 1-3/4
inches thick, mill them down to 1-1/4 inch or 1-3/8 and put two of
them together, using a vacuum bag veneer press and letting them sit
overnight” he says. “That’s why a thicker door sometimes costs more,
because it can take twice as much material and twice as much milling
time, plus the glue and time in the press.”
The woods most commonly
used are Honduras mahogany, rough fir, walnut, cherry and mesquite.
The mesquite is popular but expensive, Hausknecht says. “It has to
be either kiln dried, which costs more, or a lot of times I buy the
wood air-dried or just after it is cut. Then I have to hold it for
about a year per inch of thickness, so it will take generally two
years before I can use it. When a supplier comes by, I try to buy as
much as my budget can afford so I will have it on-hand when I need
it.”
Mesquite also has a lot
of checks and voids that require preparation, which adds to its
cost. The voids and checks are filled with a lamp black epoxy, which
doesn’t shrink when it dries. Black is used because of the strong
sunlight in the area, Hausknecht says. Mesquite changes color with
sunlight, and any other color of epoxy also would change, so over a
short period of time there wouldn’t be a match. The black filled
areas are visible and are part of mesquite’s distinctive
look.
Although Hausknecht
uses a lot of solid mesquite, he also makes his own 1/8-inch
mesquite veneer if a customer wants a plain, flush door style. For
such a door, he usually buys a manufactured solid core door with a
porous veneer on it, such as mahogany, then puts 1/4-inch MDF on
each side as a substrate for the veneer. He uses epoxy adhesive and
the vacuum bag press to lay it up.
Equipment to do the
job
Because
he does all the rough milling himself and does so many large doors,
Hausknecht has a wide range of equipment to accommodate any size
material. “There is a lot of equipment in this little shop, so I’m
not limited by the size of the wood,” he says. “I like being able to
say, ‘I can do that,’ if somebody wants something cut or a large
door made.”
Machinery includes:
10-inch and 16-inch Rockwell radial arm saws, a 10-inch Delta table
saw, a Powermatic 12-inch table saw, a 6-inch Powermatic joiner, a
16-inch-wide J.A. Fay joiner, a 14-inch Delta bandsaw, a 10-inch
Rockwell bandsaw, a 16-inch Powermatic planer and a Powermatic
hollow chisel mortising machine.
|
|
|
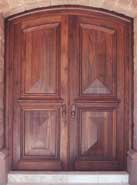 |
|
Wayne Hausknecht says this 8-foot-tall walnut door
is one of his favorites. The panels are about 2-1\4 inches
thick and the raised part is about 4 inches wide. The moulding
around the raised panels is 2-3\4 inches wide by 1-1\2 inches
thick. The center lock rail moulding came from one 7-inch-wide
solid plank and is about 2-3\4 inches thick. The hand-made
moulding around the outside is 4 inches wide. All the
components are one solid piece of wood so the grain follows
through. |
|
|
|
|
His vacuum bag press is
from Mercury Vacuum Systems, and he does all his mouldings on a
Williams and Hussey moulder. He has a Powermatic disc belt sander
and does a lot of sanding with portable power tools. He can also
rent time on a widebelt sander at other cabinet shops in the
neighborhood as needed.
Hausknecht does all his
finishing in the shop, using traditional oil-based finishes that are
brushed on. He has developed a finish system that works well in the
strong Arizona sunlight. “After I stain, I put on a base coat of
Deft exterior oil, let that soak in and wipe off the excess, to
really seal the wood,” he says. “Then I use a mixture of McCloskey
spar varnish and Water Lox, which is a really thin tung oil varnish.
They are mixed about half-and-half. I brush on a couple of very thin
coats, sanding in between, and then end with a paste
wax.”
The finish usually
lasts anywhere from six months to two years, depending on how much
direct sunlight the door is getting, Hausknecht says. With this
system, a door can be refinished easily after it degrades from the
sun.
Most of Hausknecht’s
work is residential, but he has done some commercial jobs, including
doors for local area churches. Although most of his work comes by
word-of-mouth, Hausknecht enjoys working on computers and created
his own Web site, www.wghwoodworking.com. He says that it
saves him time when people first inquire about his work — he directs
them to the Web site to see examples of his doors. This can help
screen out some prospects who might not be able to afford
him.
In the two years that
the Web site has been online, it has had over 9,000 hits, Hausknecht
says, and continues to grow. Although he is not really trying to
expand beyond his local area, he has gotten door orders from
Wisconsin and Texas through the site. “I get people worldwide
looking at it,” he says, “and it’s easier to update than my photo
portfolio. I can take photos with my digital camera and get them on
the Web site in hours if I want to.”
Although Hausknecht
does not reveal his annual sales, he says that a residential door
can easily cost $5,000 to $6,000 and up. That does not include the
door hardware, which customers choose from an outside vendor and can
cost as much as $1,500. Hausknecht estimates that he does around 10
doors each year.
While he enjoys
concentrating on doors and is not interested in doing any boxwork,
Hausknecht does do occasional pieces of furniture when customers
ask. He says he wouldn’t mind expanding in that direction sometime
in the future.
“I have always admired
people who do antique reproductions, although there is not too much
of a call for that in Tucson, that I know of,” he says. “As I get
older, though, I would like to do more hand-made custom furniture,
because the doors get heavy.”